Development of high-strength steel for automobiles
The design and manufacturing of automobiles is a very rigorous science. In order to achieve lightweighting and reduce fuel consumption while ensuring collision safety, body structure optimization and material lightweighting are essential and important means. There are many choices for lightweight materials, such as aluminum, carbon fiber, fiberglass and other materials for the body. However, due to the high cost of emerging materials and the difficulty of linking them, the proportion of traditional steel materials in the car body is still high.
According to relevant statistics, the current proportion of steel materials in automobile bodies reaches 60%-85%. Therefore, material substitution through high-strength steel is a technically mature and low-cost solution. The lightweight solution of material thinning through high-strength steel can solve the problem of high fuel consumption on the one hand and improve the safety of the car body on the other hand. The idea of using high-strength steel in automobile bodies was first proposed by the UltraLight Steel Auto Body organization (ULSAB) W-1 in 1994, with the purpose of designing a lightweight steel structural body that meets various safety and performance indicators. The first experimental body-in-white that tried to use high-strength steel was manufactured in 1998. The experimental body-in-white has the characteristics of lightweight materials and lightweight structure, low manufacturing cost and high safety. After multiple evaluations, it is believed that the ULSAB organization's attempt to use new steel grades of high-strength steel (AHSS) in automobile body design is successful. The AHSS series has a unique microstructure that utilizes complex deformation and phase transition processes to achieve an unprecedented combination of strength and ductility. AHSS is a complex and precise material. Through careful selection of chemical components and precise control of the heating and cooling processes, the comprehensive utilization of multiple strengthening methods such as phase change strengthening, fine grain strengthening, and precipitation strengthening has been achieved, making AHSS new steel bells more powerful. Ordinary low-strength steel shows higher strength, plasticity, fatigue resistance and other characteristics.
Additional projects followed to meet the requirements for improved safety and fuel efficiency through lightweighting of various vehicle structures. For example, the UltraLight Steel Automatic Closing Device (ULSAC) program develops high-efficiency hoods, doors and trunk lids using AHSS steel. The Ultra-Lightweight Steel Body Advanced Vehicle Concept (ULSAB-AVC) program further refines manufacturing methods incorporating these new materials to achieve greater mass reduction capabilities for AHSS. In 2008, WorldAutoSteel started another program called FutureSteelVehicleW-2, which accelerated the development of new AHSS grades and further improved the upper limit of strength and ductility levels. The FutureSteelVehicle (FSV) program [8] introduced the application of automotive steel into the manufacturing field of giga-pascal strength AHSS steel and increased the design size to reduce life cycle emissions, resulting in a 39% reduction in the body structure mass of the FSV.
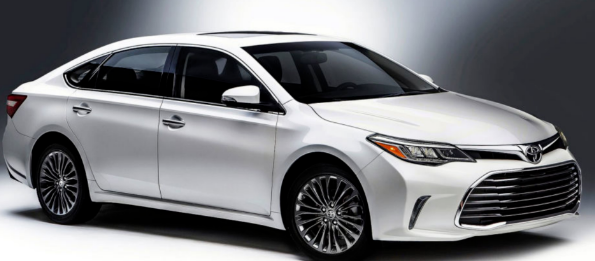
These first and second generation AHSS grades have unique properties that allow them to meet the functional performance requirements of certain parts. DP and TRIP steels, for example, have excellent energy-absorbing properties in the crash zone of cars. For structural parts of the passenger compartment, extremely high-strength steels such as martensitic and boron-based pressure hardened steels (PHS) are required to improve safety performance. Due to the successful experience of high-strength steel in car body applications, steel companies have concluded that the development trend of car body steel is towards high strength and high plasticity. According to the chronological order of the development of automotive steel, automotive steel can be roughly divided into first-generation automotive steel, second-generation automotive steel and third-generation automotive steel.
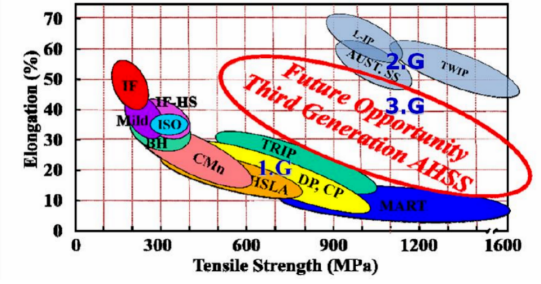
The first generation of automotive steel has a rich variety and structure, covering eight major series of automotive steel: IF steel series,
high-strength IF steel series, aluminum-killed steel series, high-strength aluminum-killed steel series, dual-phase steel series, TRIP steel series, Martensitic steel series Body steel series, bake hardened steel series. The strengthening methods of the first generation of automotive steel mainly include solid solution strengthening, grain boundary strengthening, precipitation strengthening, structure strengthening (Martensite + retained austenitic system), precipitation + structure strengthening, etc. The strength of the first generation of automotive steel covers 300~1600MPa. Its performance characteristics are that the strong plastic product is concentrated in the range of 10GPa%. If the elongation is high, the strength must be sacrificed, such as IF steel. High strength must sacrifice plasticity, such as martensitic steels. Although the first generation of automotive steel has been maturely used in the field of automobile manufacturing, its shortcomings are obvious and cannot have both strength and plasticity.
A typical representative of the second generation of
automotive steel is TWIP steel (Twin Induced Plasticity Steel). TWIP steel adds about 20% Mn to the steel to increase the stability of austenite and expand the austenite phase area, so that the phase composition of the finished product is all austenite. The austenite phase generates twin boundaries during the strain process to achieve coordinated deformation. The characteristic of TWIP steel obtaining higher plasticity due to twin boundaries is called twin-induced plasticity. Due to the excellent performance of TIWP steel, it once became a hot field of research on next-generation automotive steel. Although TWIP steel has excellent tensile properties, it has problems such as delayed fracture, high alloy content, high production cost, and difficulty in production, which seriously hinders the development of second-generation automotive steel.
Recently, research institutions in various countries have increased investment in funds, manpower and material resources to develop the "third generation products" of AHSS. These steels are specially alloyed and thermo-mechanically processed to give the "third generation products" a higher strength-ductility combination than current steel grades and the potential for more efficient joining capabilities at a lower cost . In the United States, for example, a program funded by the U.S. Department of Energy (DOE) is developing 1200MPa steel and increasing ductility threefold.